UNFORTUNATELY, it is a standard day for the Seaqual Initiative* volunteers – once again they have collected dozens of sacks of plastic waste from the Mediterranean coastline. A fantastic campaign organised by the men and women in white t-shirts emblazoned with the logo “Together for a clean ocean”.
The initiative doesn’t stop at simply collecting rubbish; the recycled plastic is the basis for the production of Seaqual Yarn, a material that is used to make the sports seats for the new SEAT** Cupra Born, for example.
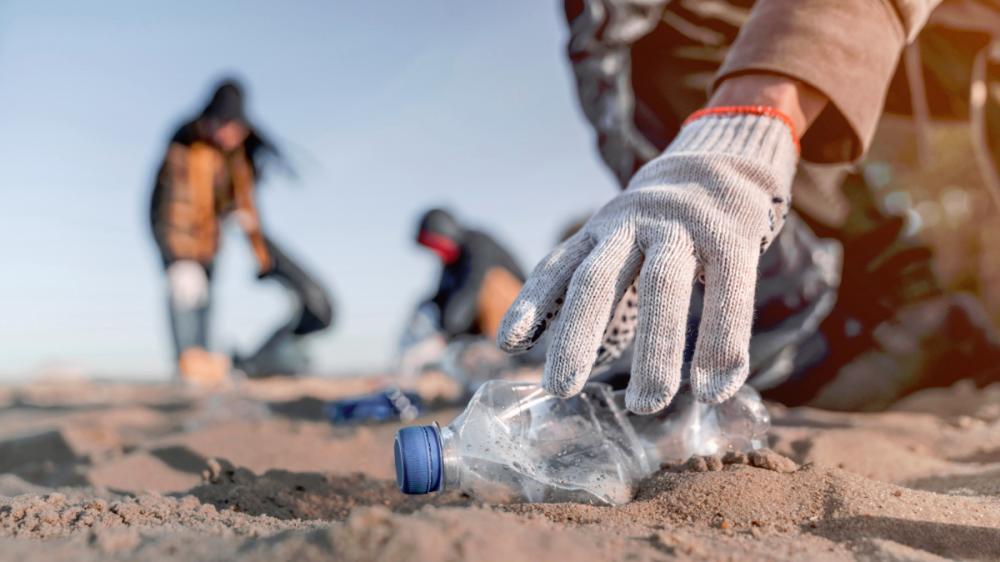
Recycling, upcycling increasingly important
This is just one of many examples from the Volkswagen Group of how cars are becoming more and more sustainable – not only when it comes to the motor. Recycling (processing and reusing raw materials) and upcycling (transforming seemingly useless waste products into materials that are as good as new) are becoming increasingly important for all of the group’s brands.
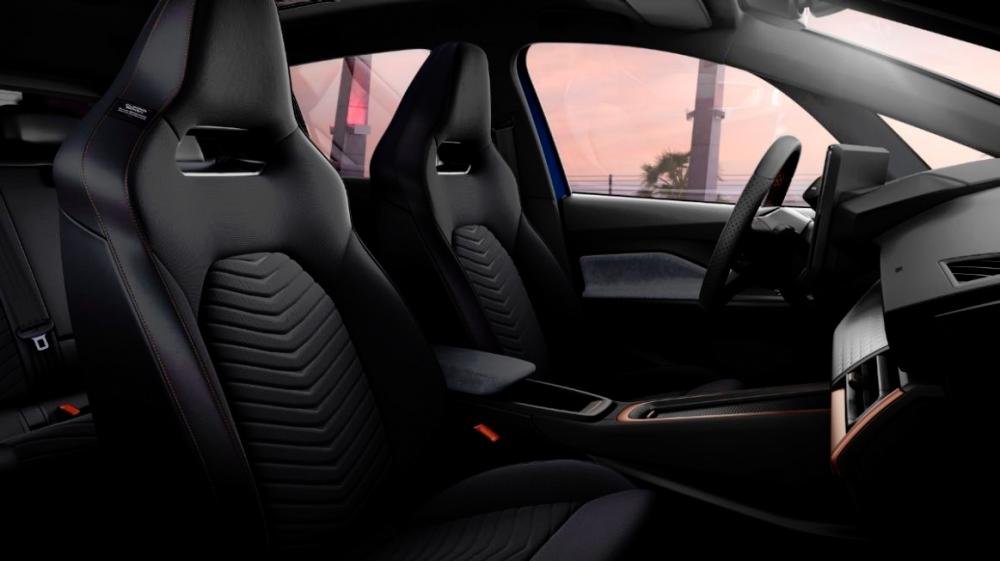
Antonino Labate is proud of the collaboration with the Seaqual Initiative: “The partnership in designing the seats for the Cupra Born shows that sustainability, innovation and modern design are a perfect fit,” said the director of strategy, business development and operations at Cupra, the challenger brand of SEAT SA.
Seaqual Yarn is a material made from recycled polymer fibres, which are obtained from the plastic waste collected. This benefits the environment – the materials for the sports seats are recycled and Cupra is doing its bit to make beaches and water cleaner at the same time.
Parts from rice husks
SEAT has always been very creative when it comes to using sustainable materials. For example, the group brand has been working on using rice husks for some time now, which are actually a by-product that is burned.
“We thought about how we could recycle this 100% plant-based raw material and developed Oryzite, a material that can be mixed and formed with other thermostable thermoplastic composites,” said Iban Ganduxe, CEO of Oryzite.
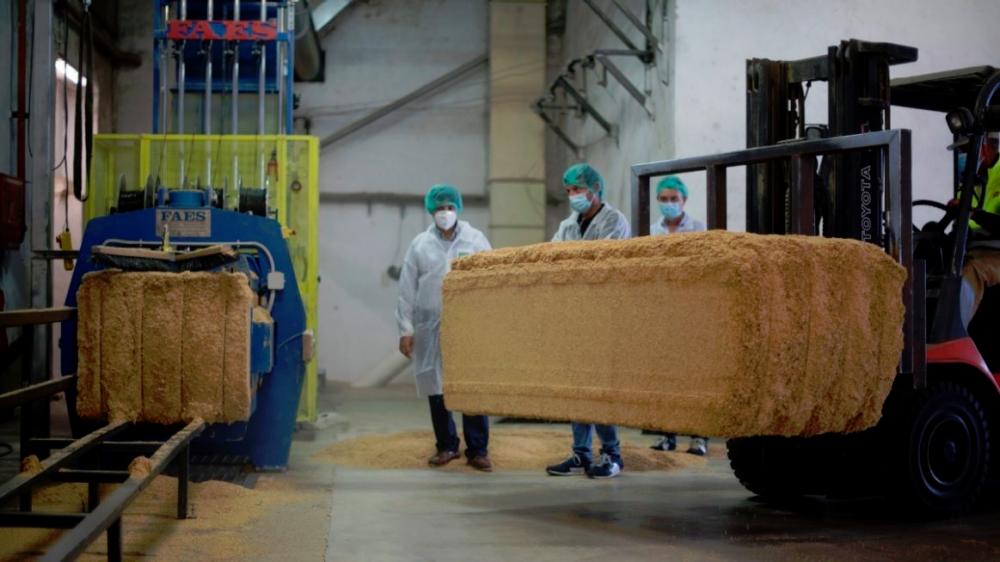
SEAT is initially trialling this compound in the production of car parts previously made from plastic, such as parts of the tailgate, the double loading floor and the roof liner. Using rice husks will significantly reduce the percentage of plastics and crude-oil-based raw materials in the vehicles.
The components are also lighter, thus reducing weight, which in turn decreases CO2 emissions. This makes the vehicles more environmentally friendly in a number of ways.
Seat covers from plastic bottles
Using sustainable materials and handling resources responsibly also play an important role at other group brands. For example, the seat covers in the Audi A3 are mostly made from recycled plastic bottles.
Broadly speaking, the process is as follows: The transparent bottles, which are easier to dye, are cleaned by a plastic recycling company and, without the screw caps, are cut up into tiny flakes in a shredder. This produces the granulate, which a yarn producer uses to spin the polyester fibres, which will become the yarn.
Up to 89% of the various textile designs for the A3 come from recycled materials – the textile “Torsion” in the Design Selection and the textile “Puls” in the S line.
For a seat trim, 45 plastic bottles with a capacity of 1.5 litres are used for the textile “Torsion”. A further 62 plastic bottles are recycled to make the carpet in the A3.
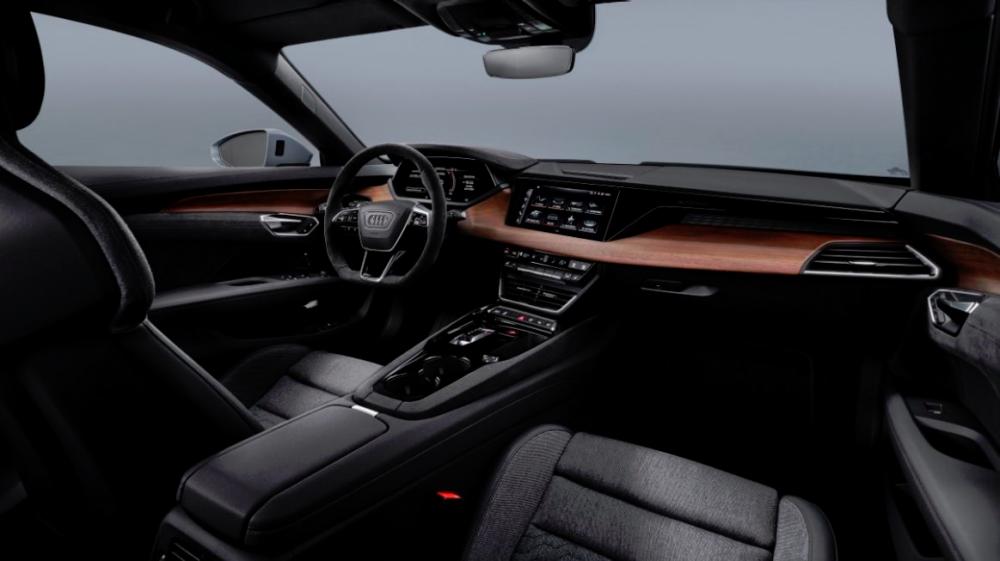
And more and more other interior components are being made from secondary raw materials, such as the insulation and absorbers, the side panel in the boot, the loading floor and the liner mats. The goal is clear – to significantly increase the percentage of recycled materials in the Audi fleet in the coming years. In doing so, the premium brand will continue to provide their customers with the high-quality products they are used to.
The Ingolstadt-based brand also leads the way in other areas; as part of a pilot project for the Audi e-tron GT01, the company is sourcing 20-inch rims from aluminium produced with reduced CO2 emissions, which (aluminium-producing giant) Alcoa supplies to the Ronal Group, who manufacture the wheels. The key feature – during the custom-developed, innovative smelting process, oxygen is released instead of carbon dioxide.
Non-leather fittings, primarily made from recycled materials, are also available for the Audi e-tron GT. The covers for the bucket seats plus come in either a combination of imitation leather with the textile Kaskade, or a mix of imitation leather with the microfibre material Dinamica.
Both cover options predominantly consist of materials such as polyester fibres, which are manufactured from recycled plastic bottles, textiles or residual fibres – there are 119 recycled plastic bottles in every Kaskade cover trim.
Dinamica also covers the top of the centre console, the door trims and the cover for the dashboard. The carpet and floor mats in the e-tron GT are usually made from Econyl – a material produced entirely from recycled nylon fibres. It is made from production waste, fabric scraps, old carpets and old fishing nets.
Flax fibres, olive leaves for Porsche
The Porsche brand is another pioneer – for more than two years, the company based in Zuffenhausen has been manufacturing both the doors and the rear wing of the Porsche 718 Cayman GT4 Clubsport MR racing car using a mix of natural fibres that is primarily sourced from renewable raw materials.
Now, additional prototype components are currently undergoing testing in racing action. These include the front and rear apron, front spoiler lip, front and rear lids, mudguards and diffusor, including the aerodynamic fins, which are also made from this regenerative material.
These sustainable organic fibre composites are made from flax fibres, which are produced in agriculture – without compromising food cultivation.
When it comes to production vehicles, the Porsche Taycan02 is one that stands out in terms of sustainable materials – in the interior, the sustainably tanned club leather “Olea”, which uses olive leaves as tannins, is available as an alternative to traditional leather.
*Seaqual Initiative is “a community with a single voice against plastic pollution. We bring together individuals, organisations and companies to help clean our oceans, raise awareness of the issue of marine plastic and highlight the heroes who are working to solve it”.
**SEAT, the acronym for Sociedad Espanola de Automoviles de Turismo, is a Spanish car manufacturer, which sells its vehicles under the SEAT and Cupra brands. Based in Barcelona, it is a wholly-owned subsidiary of the Volkswagen Group.
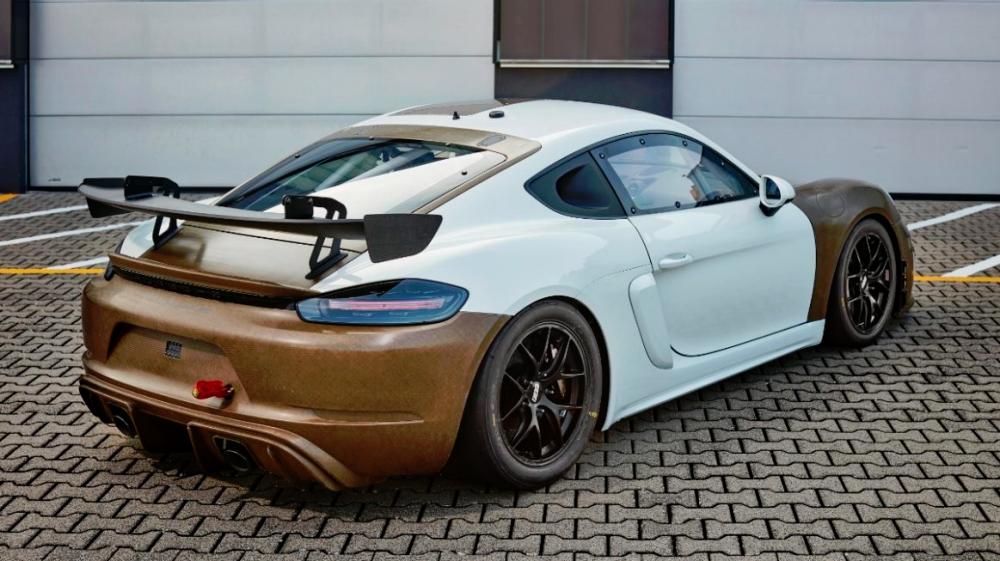